As a research project with Tiipoi, a London based industrial design studio, I created and tested some custom clay bodies using refractory waste.
Tiipoi has access to industrial ceramic waste of which there is an estimated 35-55 tonnes in a 2km radius of Tiipoi’s workshop, in Peenya, an industrial area in Bangalore. The intent was to create a clay body that largely consists of fired ceramic waste - ground down to an 80 mesh powder, that acts like grog.
The pieces will be brought to life by Tiipoi’s very own potter, Khanmung Sasa, who hails from an award-winning family who practice the tradition of Longpi black pottery. Sasa will be using his expertise to improvise a new moulding technique that is suitable for these types of moulds.

We first started by adding some terracotta to the existing clay mix - used to make refractory ceramic spacers - in a press mould. The consistency of this clay is like crumbly, and the colour a clinical white. We added some terracotta and about 5-7% grog to the mix to make it pliant and a more interesting texture + colour (see above, right-most test tiles).
With these successful trials, we attempted to add more grog, but for the same, a custom recipe had to be tried out. The following are the findings for the same.
clay body | shrinkage % cone06 | shrinkage % cone6 | observations |
---|---|---|---|
Type 01- 30% grog + 30% terracotta + 30% ball clay + 10% silica | 4 | 8 | brittle; less elasticity |
Type 02- 30% grog + 30% terracotta + 20% ball clay + 10% silica + 10% bentonite | 5 | 8 | workable for production; roll out slabs + press into moulds |
Type 03- 40% grog + 20% terracotta + 20% ball clay + 10% silica + 10% feldspar | 1 | 6 | brittle; crumbling when used |
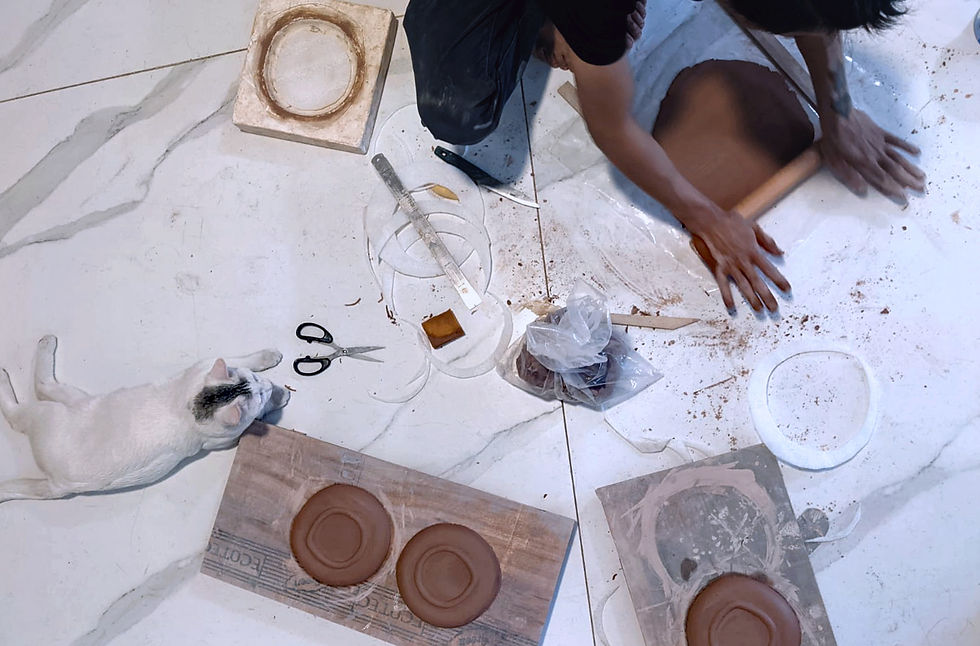
Comments